АВТОМАТИЧЕСКАЯ КОНВЕЙЕРНАЯ ЛИНИЯ
Автоматизированный комплекс нанесения порошковых покрытий, дает бесспорное преимущество в скорости выполнения работ, высвобождает людские ресурсы, увеличивает производительность и качество выпускаемой продукции. Автоматическая линия порошковой окраски состоит из разных составных частей технологического оборудования: тоннеля подготовки поверхности изделий, камеры сушки и камеры нанесения порошкового покрытия, печи полимеризации, соединенных между собой автоматическим подвесным конвейером непрерывного действия.
СОСТАВ И КРАТКОЕ ОПИСАНИЕ ТЕХНОЛОГИЧЕСКИХ ЭТАПОВ НА ЛИНИИ ОКРАСКИ
Автоматическая линия нанесения порошковых покрытий, относится к категории сложное оборудование, состоящее из комплекса взаимосвязанных компонентов.
Исполнение автоматических линий нанесения защитных покрытий, возможно разных типов и конфигураций в зависимости от многих факторов и технологических задач, отдельно взятого производства. Каждый проект линии окраски, является индивидуальным решением.
Тоннель мойки изделий
Печь сушки изделий
Циклонная камера нанесения
Печь полимеризации
БЛОК НАГРЕВА ПОЛИМЕРИЗАЦИИ
Нагревательный блок (косвенного типа) монтируется в определенной части к корпусу печи полимеризации. Камера сгорания изготовлена из специальной марки нержавеющей стали. Конструкция секции изготовлена таким образом, чтобы получить три хода дымовых газов перед выходом их в атмосферу, получив таким образом максимально высокий КПД. Корпус нагревательного блока изолирован теплоизоляционными панелями толщиной 150 мм из каменной ваты. Горячий воздух из теплообменника равномерно распределяется по печи с помощью регулируемых воздушных каналов из оцинкованной стали 1,5 мм. Теплообменник в купе с циркуляционными вентиляторами совместно с системой воздуховодов, расположенных внутри печи, обеспечивают подачу нагретого воздуха и равномерное его распределение внутри всего объема печи полимеризации.Теплообменник комплектуется горелками под разные типы энергоносителя, по желанию можно выбрать горелки, по предпочтению к бренду.
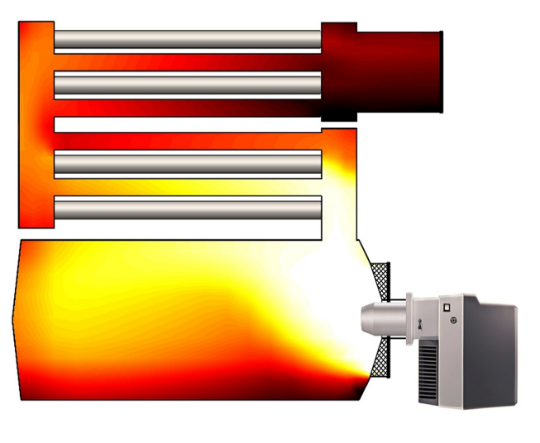
ВОЗМОЖНОСТЬ ВЫБОРА ТИПА НАГРЕВА И МАРКУ ГОРЕЛКИ
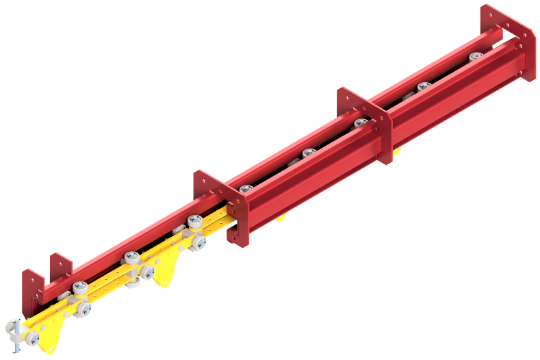
ПОДВЕСНОЙ МОНОРЕЛЬСОВЫЙ КОНВЕЙЕР (КАРДАННОГО ТИПА)
Перемещение изделий на конвейере, обеспечивается несущими и направляющими звеньями цепи, двигающейся по замкнутому подвесному монорельсовому пути, благодаря способности гнуться как в вертикальной, так и в горизонтальной плоскостях. Изделия, подвешиваются на подвески или на специальные грузонесущие элементы (на шарнирной или жесткой подвеске), проходят через все этапы технологического процесса до момента разгрузки.Направляющие конвейера изготавливаются из листовой стали ST 37 толщиной 3мм, для фиксации и монтажа направляющих используют фланцы и болтовые соединения.
КАК МЫ ПОДБИРАЕМ КОНВЕЙЕР
Что следует учитывать при выборе конвейера для окраски лакокрасочными материалами:
Размер и вес окрашиваемых деталей
Тип конвейера, выбранного для покраски ваших деталей, будет зависеть от веса, размера, толщены и даже формы транспортируемых изделий, а также от способа применяемого процесса покраски.
Тип материала, из которого изготовлена деталь (металл, пластик, дерево и т. д.)
В зависимости от требований по окраске определенных типов изделий, для обеспечения особых стерильных условий конвейер может быть перевернут (прорезь вверх, специальные лотки) или установлен боком. Такая установка конвейера гарантирует, что никакие капли из держателя детали или носителя не будут соприкасаться с окрашенными деталями.
Каким образом предполагается навешивать изделия к подвесному конвейеру
Для удобства навески и снятия изделий, отталкиваясь от их особенностей (вес, тип, габариты), мы можем предложить от простейшего опуска конвейера в зонах навески и съема изделий, до специальных автономных или интегрированных в конвейер приспособлений, позволяющих без лишних усилий навешивать и снимать изделия.
Расположение технологического оборудования в составе линии окраски (печи, погружные резервуары, камеры нанесения, участвующие в процессе)
Конструктивные элементы конвейера (направляющие, цепь, подвески, крепеж) должны выдерживать температуру до 350 градусов во время прохождения через печь полимеризации. Выдерживать жесткие химические вещества, используемые во время процессов промывки, обезжиривания, дегазации и пескоструйной обработки. Конвейер в зависимости от технологических задач, частично может располагаться в разных плоскостях (стадия окунания, подъемы, опуски и повороты).
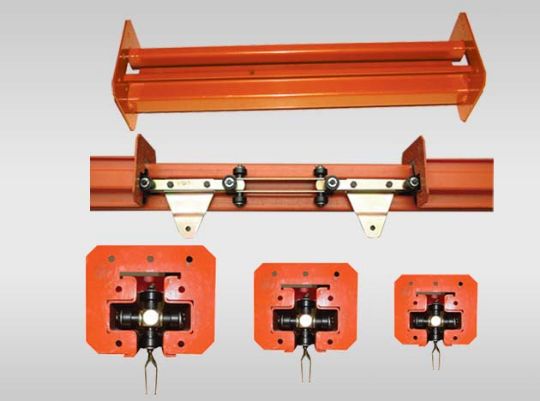
НАПРАВЛЯЮЩИЕ КОНВЕЙЕРА
При проектировании линии покраски, подбирается необходимый тип конвейера, способного выдержать весовые нагрузки и температурные перепады. В основном используют 3 типа конвейера: Легкий тип 30кг/точку, Средний тип 60 кг/точку, Тяжелый тип 120 кг/точку.
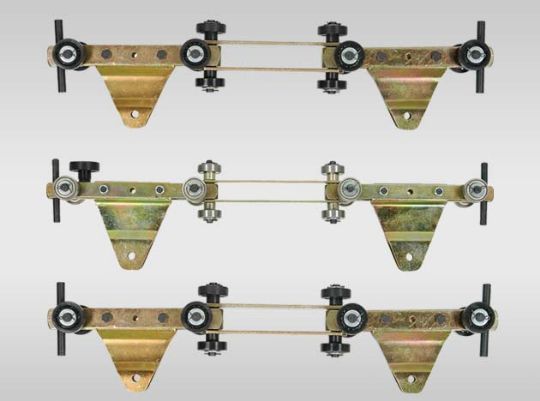
Бипланарные цепи
Бипланарные цепи изготавливаются с интервалом между звеньями цепи – 180мм х 220 мм, расстояние между осями подвесок 400мм. Звенья крепятся между собой при помощи крестовидных штифтов, подшипники фиксируются при помощи шпильки с шайбой.
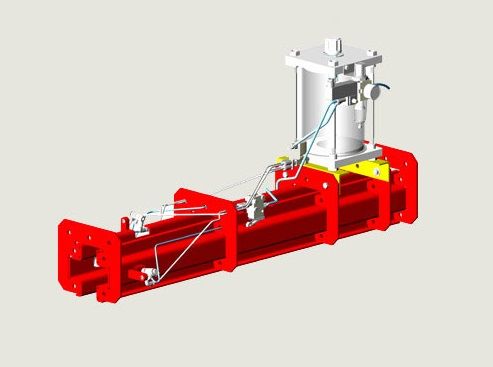
Блок автоматической смазки
Позволяет смазывать аэрозольным способом 4 подшипника цепи, за раз. Подшипники цепи конвейера смазываются в автоматическом режиме, проходя через данный узел. В системе смазки используется высокотемпературное масло, определенной консистенции.
Подвески и грузонесущие элементы
Огромное число приспособлений разработано для установки на роликовые решения, что позволяет использовать их для механизации широчайшего диапазона производственных процессов.
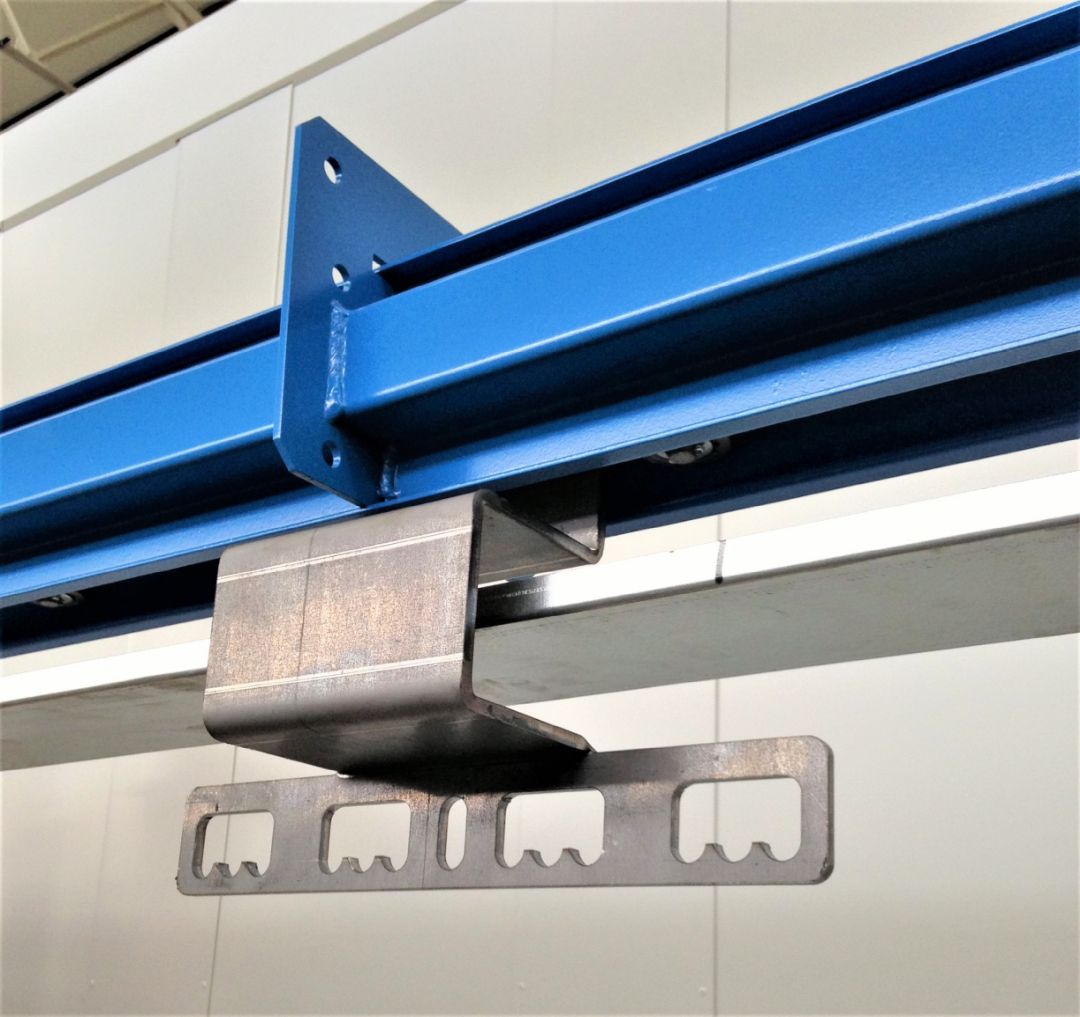
Лоток от осыпания
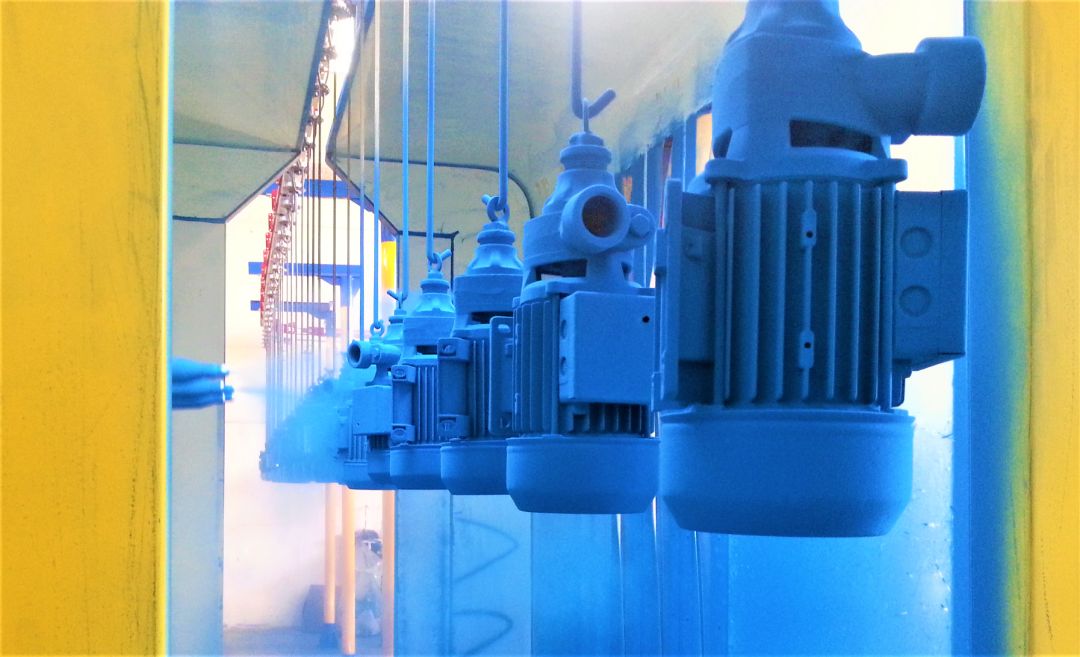
Вращение в камере
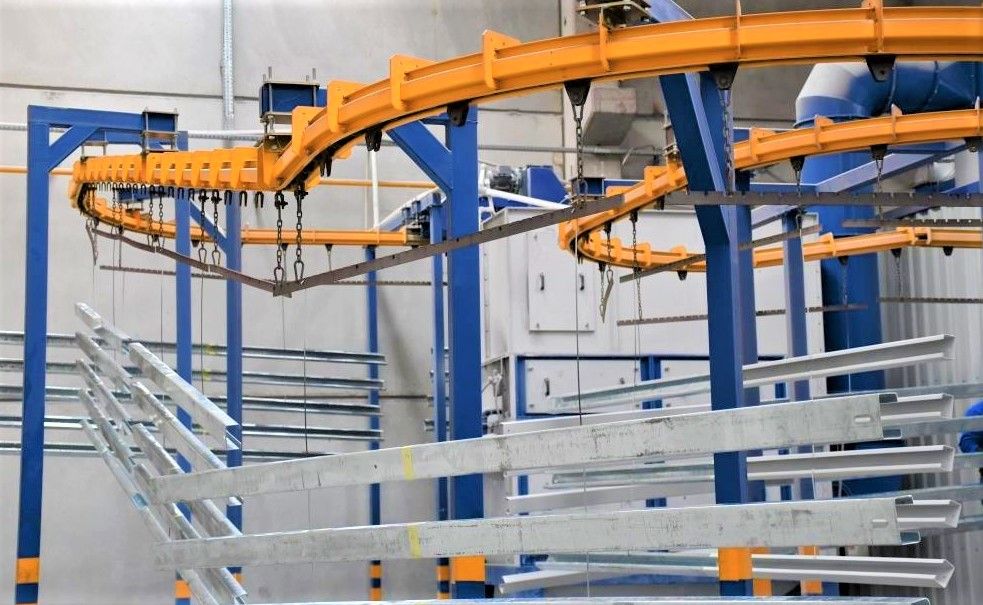
Произвольные подвески
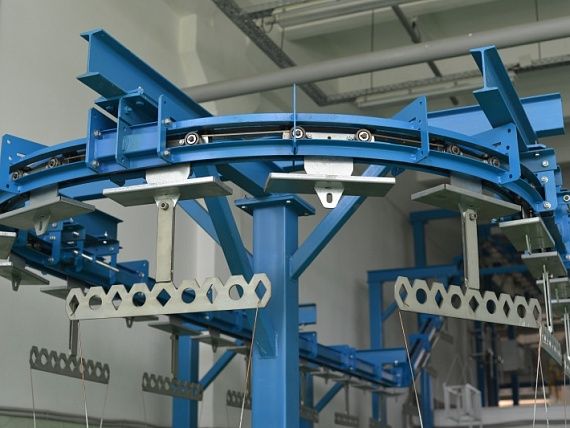
Зонт над подвеской
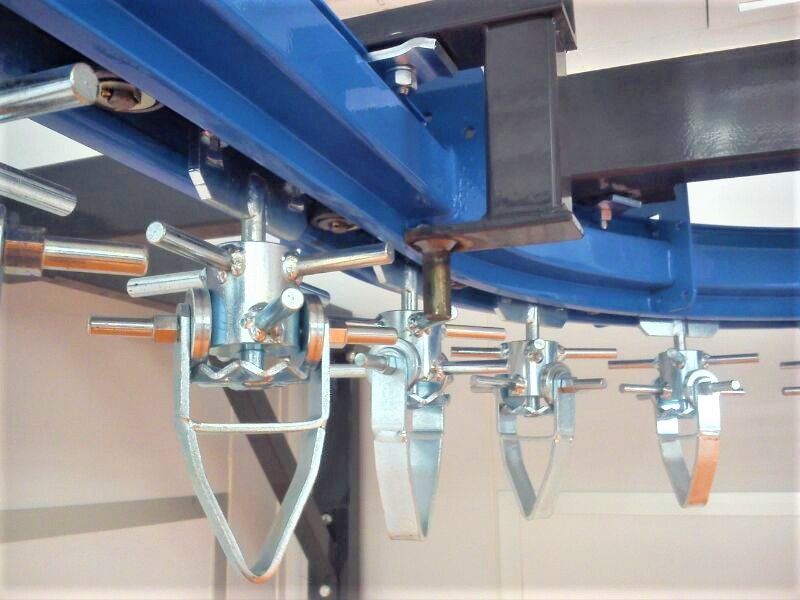
Тактовое вращение
панель управления
Весь покрасочный комплекс питается от одной панели управления. В самом шкафу управления, а также между всеми элементами линии в качестве соединительной проводки используются материалы брендов Siemens и Schneider Electric. Проводка находится в надлежащих секциях и прошла сертификацию ТSE. Все функции покрасочной линии контролируются и управляются с главной панели.
ПРОГРАММИРУЕМЫЙ КОНТРОЛЛЕР SIEMENS S7
Управление процессами автоматизации линии происходит по заданному алгоритму программного обеспечения. Контроль и настройка процессов осуществляется оператором на панели управления с PLS экраном.
Дистанционный контроль работы оборудования
Дистанционный контроль обеспечивает передачу сигналов в случае сбоя в работе линии, что позволяет отслеживать состояние ключевых технологических процессов и предоставлять важные рекомендации сервисной службе клиента.
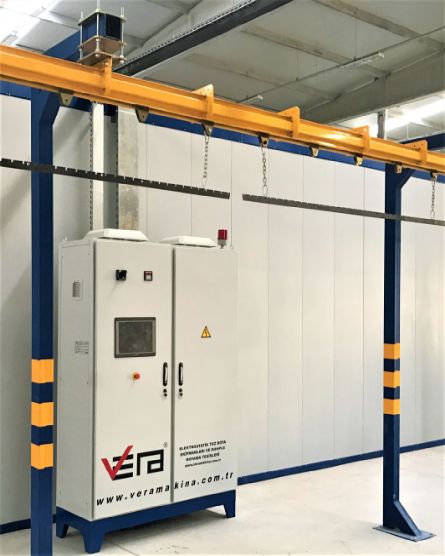